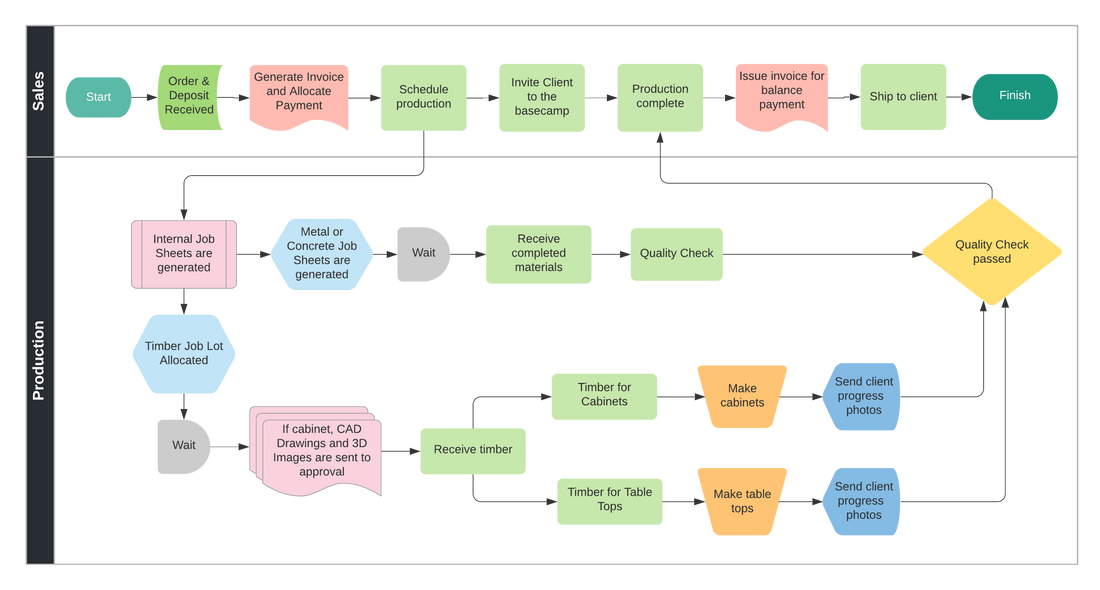
The Process for Ordering Custom Furniture
Share
Custom furniture offers a unique blend of personalisation, craftsmanship, and quality that is unmatched by mass-produced pieces.
However, the process of ordering custom furniture can seem daunting if you're unfamiliar with it.
At Lumber Furniture, we've streamlined this process to ensure a smooth and enjoyable experience for our clients.
This blog will outline each step involved in ordering custom furniture, from the initial order to delivery, providing detailed information on what to expect.

How long does it take to make custom furniture?
It generally takes 10-14 Weeks to have a solid timber custom piece made. Live Edge Slab tables, however can take up to 18 weeks due to the complexity of the work.
1. Order and Deposit Received
The journey begins when you place your order. At this stage:
- Consultation: We discuss your requirements, including design preferences, materials, dimensions, and any specific features you want.
- Quotation: Based on the consultation, we provide a detailed quotation outlining the costs involved.
- Deposit: To secure your order, a 70% deposit is required. This deposit confirms your commitment and allows us to start the next steps.
2. Generate Invoice and Allocate Payment
Once the deposit is received:
- Invoice Generation: We generate an official invoice detailing the deposit and the remaining balance.
- Payment Allocation: The deposit is allocated towards your order, ensuring your funds are correctly tracked and applied.
3. Invite Client to Basecamp
Basecamp is our project management tool that keeps you informed throughout the production process:
- Invitation: You receive an invitation to join Basecamp.
- Communication: Through Basecamp, you can communicate with our team, ask questions, and stay updated on your project's progress.
- Documentation: All relevant documents, design specifications, and progress updates are shared here.
4. Schedule Production
Scheduling production involves several sub-steps to ensure everything is in place for crafting your custom piece:
4a. Internal Job Sheets Are Generated
- Detailed Plans: We create detailed job sheets for our craftsmen, outlining every aspect of your order.
- Task Allocation: Specific tasks are assigned to the relevant team members based on the job sheets.
4b. Timber Allocated
- Timber Selection: We select the best quality timber based on your specifications.
- Preparation: The timber is prepared and allocated to your project, ensuring we have everything needed to start production.
4c. Metal Job Sheets Created
For pieces involving metal components:
- Design Specifications: Detailed metal job sheets are created, specifying the design and dimensions required.
- External Collaboration: If necessary, we collaborate with trusted metalworkers to produce these components.
4d. Receive Completed Metal Parts
Once the metal parts are completed:
- Inspection: We inspect the metal parts to ensure they meet our quality standards and match the design specifications.
- Integration: The parts are then integrated into the production process for your furniture piece.
4e. Quality Check
Before moving forward, we conduct a thorough quality check:
- Inspection: Every component, including timber and metal parts, undergoes a meticulous inspection.
- Approval: Only after passing this quality check does the production process continue.
5. Timber Parts Made (e.g., Cabinet or Tabletop)
Crafting the timber parts involves several steps:
- Cutting: The timber is cut to the specified dimensions.
- Shaping: Each piece is shaped according to the design, whether it's a cabinet, tabletop, or other components.
- Sanding: The pieces are sanded to achieve a smooth, even surface.
- Assembly: The parts are assembled to form the basic structure of your furniture piece.

6. Send Client Progress Photos
We believe in keeping you informed and involved:
- Progress Updates: We send you photos of your furniture at various stages of production.
- Feedback: You can provide feedback or request minor adjustments if necessary.
7. Production Complete
When production is complete:
- Final Inspection: A thorough final inspection ensures the piece meets all quality standards.
- Finishing Touches: Any final touches, such as additional sanding or finishing, are applied to perfect the piece.
8. Issue Invoice for Balance Payment
Before delivery:
- **Invoice Generation**: We generate the final invoice for the remaining balance.
- **Payment**: You complete the payment, which allows us to prepare for delivery.
9. Ship to Client
The final step is getting your custom furniture to you:
- Shipping: We arrange for delivery to your specified address. For clients in Melbourne, Sydney, Adelaide, and Canberra, we offer delivery and installation services.
-Installation**: Our team ensures your furniture is correctly installed and positioned in your home.
Flow Chart Diagram
This flow chart provides a visual representation of the steps involved in the custom furniture ordering process, making it easier to understand each stage.
Ordering custom furniture is an exciting journey that results in a unique piece tailored to your specifications.
At Lumber Furniture, we pride ourselves on our transparent and customer-focused process. By following these detailed steps, we ensure that every piece we create meets the highest standards of quality and craftsmanship. If you're ready to start your custom furniture project, contact us today to begin the journey.
For enquiries, email us at enquiries@lumberfurniture.com.au or follow us on Instagram @lumber_furniture, Facebook @lumberfurniture, and Pinterest at Lumber Furniture
https://www.pinterest.com.au/Lumberfurniture